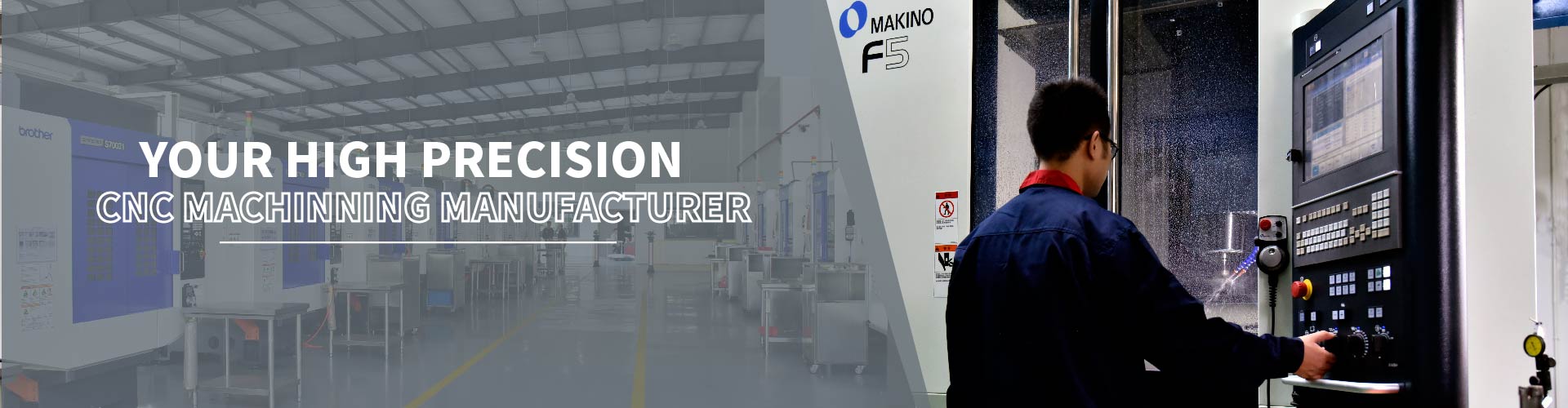
WHY SUNRISE CAN BE YOUR PREFERRED SUPPLIER?
Sunrise Metal focuses on Aluminum precision CNC machining service for over 10 years. We can not only machine your die casting parts but also help you make purely machining parts.
- We provide cost-effective solutions by DFM & feasibility analysis.
- Our facility owns a precision & high-efficient machining center.
- We offer various surface treatments service for you.
- Our precision measuring equipment & quality control ensure the highest quality products.
WHAT PRECISION MACHINES WE HAVE
HOW SUNRISE GUARANTEE YOUR PROJECT QUALITY
Our quality policy is customer satisfaction & continually improving. As an IATF 16949 & ISO13485 certified supplier, we continually improve our manufacturing quality and organization at a higher level.
Our lab equips precision measuring tools such as Carl Zeiss CMM, Spectrometer, etc to
assure you of good quality machining parts. We’ll continually invest in spection instruments and training our staff.
Our rich-experienced QC team use core tools (APQP, FMEA, PPAP, MSA SPC) to ensure high quality production parts. We keep strict quality control from 1st article inspections, in-process inspections, and final inspections.
INDUSTRIES SUNRISE SPECIALIZED IN
WHAT SURFACE FINISHING WE CAN OFFER
For your machined parts, we can offer a 1-stop precision CNC machining service, including surface treatments like Anodizing, Chromate, Powder coating, wet painting, E-coating, Plating, Silk printing, etc.
All our parts are meet ROHS and REACH requirements.
- Precision CNC Machining Equipment List
- Premium Quality Measuring Equipment List
With high-efficiency automated processing machine centers, we equip various axis (3 & 4 & 5 & 7 axes) machines to meet your different parts demand. Our precision CNC machines like the Makino F5 brand will help you produce close tolerance parts.
No. | Name | Stroke | Q’ty |
1 | Makino F5 CNC machine | 900*500*450MM | 1 |
2 | Mazak 7-axis turning&milling machine | Ø658*1011MM | 1 |
3 | Mazak /Hass 5axis CNC machine | Ø850/Ø600 | 4 |
4 | 3-axis CNC machine center | 2000*1500MM | 1 |
5 | 4-axis CNC machine center | Ø250*800MM | 8 |
6 | 3-axis CNC machine center | 1000*600*600MM | 20 |
7 | CNC Lathes | Ø320*800/Ø610*1000MM | 2 |
8 | Sodick Wire cutting Machine | 400*400*200MM | 3 |
9 | EDM machine | 500*400*400MM | 2 |
10 | Surface grinder | 600*300*200MM | 1 |
We have a laboratory to allow for measuring the product characteristics. By also verifying product quality via Carl Zessis CMM, x-ray, spectrometry, particle inspection, and other required tests including cleanliness, leakage, salt spray, etc.
You can expect the highest possible quality in Sunrise.
No. | Name | Brand | Q’ty |
1 | CMM | Carl Zessis | 1 |
2 | CMM | SanYou | 1 |
3 | Spectrometer | China | 1 |
4 | Microscope | China | 1 |
5 | Projector | China | 2 |
6 | X-ray Detector | SANDT | 1 |
7 | Cleanliness Test Equipment | China | 1 |
8 | Leakage Test Equipment | China | 2 |
9 | Salt Spray Testing Equipment | China | 1 |
10 | Pneumatic Measuring Instrument | China | 2 |
11 | Hardness Testing Machine | China | 1 |
12 | Color Meter Machine | China | 1 |
13 | Thickness Testing Machine | China | 1 |
14 | Electronic Balance | China | 1 |
15 | Density Balance | China | 1 |
CNC MACHINING HANDBOOK
CNC Machining is a subtractive manufacturing process where the material is removed from a solid piece or block. It’s a very popular manufacturing technology all over the world.
In this handbook, we’ve discussed in detail various aspects of CNC Machining. You can get a proper understanding of any chapter you’re interested in by clicking the jump links in blue.
CNC MACHINED ALUMINUM PARTS ARE THE BEST ALTERNATIVE TO STEEL
ENSURE HIGH-QUALITY AT A BUDGET WITH CNC MACHINED ALUMINUM PARTS
Aluminum is an excellent material choice for making CNC machined products. Aluminum’s economy, lightweight, and durability has quickly made it one of the most used metals all over the world.
Aluminum’s exceptional material properties and widespread availability has been a major influence for the sudden growth in demand for CNC Machined Aluminum Parts. Many conventional materials are now being replaced with aluminum parts.
With the rapid advances in CNC Machining technologies, the production of machined aluminum parts are becoming more and more efficient and cost-effective. So, the application of aluminum parts is expected to rise more in the recent future.
ADVANTAGES OF CNC MACHINED ALUMINUM PARTS
CNC machining of Aluminum is preferred over various other metals for its multitudes of benefits. Although some of the perks will vary for different Aluminum alloys. The main advantages of CNC Machined Aluminum Parts are discussed in detail below.
Lightweight
CNC Aluminum Parts are very light. Aluminum has a specific gravity of 2.7, which is multiple times lighter compared to cast iron. So, Aluminum parts are an excellent choice for Automobiles, airplanes, etc. where lighter parts play a big role in performance.
Good Mechanical Strength
Despite Aluminum parts being lighter, they have an exceptional strength-to-weight ratio. So, CNC Aluminum Parts can be used for heavy-duty applications with high strength requirements.
Easy to Machine
Aluminum is very easy to machine compared to steel. So machining parts need less expensive tools and consume less energy. Thus machined Aluminum parts will be more cost-effective to manufacture.
Corrosion Resistant
Corrosion resistance is one of the best things about Aluminum machined parts. Due to their excellent corrosion resistant nature, they are often a more suitable option. They can be used in harsh corrosive conditions without any worries.
High Weldability
Aluminum alloy parts have good weldability as well. Although that mostly applies for Aluminum alloys with moderate strength. Some high strength varieties of Aluminum alloys usually have less weldability compared to the others.
Allows Heat Treatment
Unlike die cast Aluminum parts, CNC Aluminum parts can be heat treated. So, their mechanical properties can be further improved for gaining higher strength. That really diversifies the application of CNC Aluminum Parts.
Exceptional Conductivity
Aluminum parts have very good electrical and thermal conductivity. They provide excellent shielding when used as network device housing. The aluminum part’s high heat dissipation and thermal conductivity allow better heat management in electronic devices.
Economical
Aluminum is a common metal that is available all over the world. So, the raw material is cheaper than most other metals. So, manufacturers are able to produce more economical yet high-quality products for consumers.
Best Aluminum Alloy for CNC Machining
Various parameters are considered when determining the utility of a metal alloy. Numerous Aluminum alloys are available in the market with slight variations of alloying elements such as Zinc, Magnesium, Iron, Copper, etc.
Each alloying element enhances some properties that Aluminum was initially lacking. Sometime that could compromise Aluminum inherent good properties a little bit as well. Each type of alloy is aimed for a different type of applications.
So, a deep understanding of material properties is necessary to determine which Aluminum is suitable for a certain task. When it comes to CNC Machining Aluminum 6061 Alloy can be considered the best.
Aluminum 6061 (A6061) Alloy is by far one of the most balanced alloys for CNC Machining. It is a precipitation-hardened alloy with a good percentage of magnesium and zinc. It is widely used for general and structural applications.
The main features of A6061 alloy are described below.
- Has very good machinability
- Has excellent mechanical strength
- Offers the best corrosion resistance
- Exhibits high weldability
- Parts can be heat treated
So, for these special properties, Aluminum 6061 alloy is most commonly used for the production of CNC machined parts. Here’s a chart of the basic material properties of A6061 Alloy.
APPLICATION OF CNC MACHINED ALUMINUM PARTS
CNC Machined Aluminum Parts are widely used in many sectors. Aluminum parts have gained huge popularity recently and become a preferable alternative for steel and iron parts. Some common application of Aluminum parts is discussed below.
Transportation
The transportation sector has a massive demand for CNC Machined Aluminum Parts. The global concern regarding saving energy has led manufacturers to choose lighter aluminum parts for better fuel economy. Vehicles, aircraft, and ships are using aluminum parts as a strong and lighter alternative to steel.
Consumer Electronics
Aluminum’s exceptional thermal and electrical conductivity has made it very popular in consumer electronics. Many consumer electronics such as laptops, smartphones, televisions, and accessories are using aluminum CNC parts for ensuring better quality.
Medical Devices
Precision aluminum parts are an indispensable thing for the medical industry. Extremely precise parts are required for most medical devices. It is quite impossible to manufacture parts with such precision without CNC Machining.
DESIGN CONSIDERATION FOR CNC MACHINED ALUMINUM PARTS
How you design your parts have a significant impact on your CNC precision machining process. Following some guidelines can reduce your machining time, machining cost, and difficulty. Here are some important tips about parts design.
- CNC Machining cost greatly depends on the time required for machining. So, Keep it simple, avoid any unnecessary details that may hamper the machining process.
- Complex parts may require the parts to be divided into multiple segments. Divide it in a manner so that it doesn’t need to be rotated as much.
- All Edges should be given fillet. Try to use fillets of the same radius.
- Avoid thin walls and deep pockets if possible. They require very careful programming and frequent tool changes to avoid damaging the parts.
- Feasibility Study, it is very important to discuss with your CNC precision machining supplier to make the parts feasible for manufacturing.
You can know more about Sunrise Metal’s CNC machining capability when you need to select a CNC precision machining China supplier.
CNC Machining Handbook
Chapter 1
Introduction
CNC (Computer Numerical Control) machining is a popular manufacturing technology that manufacturers all over the world use. They manufacture different parts of various instruments using this technology. CNC machining is a subtractive process where materials omit from a solid piece or block by following a CAD model.
CNC machines use various cutting tools to remove the material. The size and shape of the cutting tool depend on the type of the CNC machine. The CNC machining technology can shape a large variety of materials such as Steel, Bronze, Copper, Aluminum, Titanium, and also different types of plastics such as Nylon, ABS, etc.
CNC machining can form parts with both simple and complex creative designs. The whole CNC machining technology has three main principles such as:
- Designing CAD Model
- Generating G-Code, and
- Executing Machine Operation
An expert must supervise all these tasks.
History of CNC Machining
The lathe machine is the first machine that created an object or part. Manufacturers created an object in the shape of a bowl using that lathe machine in 700 B.C. in Italy. That was manual and also handcrafted machining.
After that in the 18th century, the first automated machining was used which was powered by steam. That machining technology was mechanical.
In the late 40s, MIT took the initiative to develop a programmable machine known as the NC (numerical control) machine. Each movement of that machine was encoded by punch cards.
In the 50s and 60s, the programmable machines achieved more precision by the developers and also changed the fate of manufacturing industries. The advanced version of the programmable machine is called the CNC machine.
In this era, CNC machining has become a blessing for modern technologies. Nowadays, robotic technologies are collaborating with CNC machining technology.
Today, manufacturers can make more complex designs using multi-axis CNC machining technology. The number of tools is increasing and also the time complexity is reducing. The computerized code can control the motion of the tools. The machine has become faster and also the parts were more accurate.
The Advantage and Disadvantage of CNC Machining
CNC Machining has both benefits and drawbacks. The section below shows these benefits and drawbacks:
Advantages/Benefits
- CNC machining has increased the production capacity of industries. This machine works continuously all over the day, all over the year.
- No matter how many items or products are manufactured, the shape, as well as the features of those manufactured items, always remain the same.
- There are several types of CNC machines. Less-trained people can also operate some types of CNC machines.
- CNC machines can be developed by changing or updating software drivers.
- Engineers can be trained by using virtual software of CNC machines where they can practice the CNC machine operation.
- Many items that cannot be made using manual machines, can easily be made using CNC machining.
- CNC machines can use various advanced software such as Pro/DESKTOP which are very useful to make complex designs.
- Using this modern software, engineers can simulate the production of their creative ideas. They don’t need to build a model or prototype for that. It reduces costs and also saves time.
- Multiple machines can be supervised by only one person at the same time.
Disadvantages/Drawbacks
- CNC machining technology is costlier than manually operated machines. With the flow of time developers are trying to reduce the cost.
- Multiple axis CNC machines are more complex to operate. Experts and also trained engineers are needed to operate those types of CNC machines.
- As technologies are developing very fast, old training skills are not adequate for running the CNC machines.
- Multiple CNC machines can be operated by only one skilled person. It increases the unemployment problem.
Difference Between 3D Printing and CNC Machining
There are some significant differences between CNC machining and 3D printing such as:
3D Printing | CNC Machining |
3D printing is an additive process that builds a part or item layer by layer using materials. It adds small parts and then forms a big part. | CNC machining is a subtractive process that removes material from a solid block and then forms a particular shape. |
3D printing is a more recent technology than CNC machining. It was primarily limited to Resins and Thermoplastics. But, technological advancement has made metal 3d printing possible as well. | CNC machining is a much older and more established technology. There is a wide range of material choices for CNC Machining. |
A 3D printer is easier to use than a CNC machine. | A CNC machine needs more expert people than a 3D printer to operate. |
The amount of waste material in 3D printing is less than CNC machining. | The amount of waste material in CNC machining is more than the 3D printing. |
3D printing tools are less standardized than CNC machines. | CNC machining tools are more standardized than the 3D printer. |
3D printing has fewer design restrictions than CNC machining. | CNC machining has more design restrictions than 3D printing. |
It Provides less accuracy and precision than CNC machining to the parts. | It provides more accuracy and precision than 3D printing to the parts. |
The features and mechanical properties of the built parts are not as good as CNC machining technology. | The features and mechanical properties of the built parts are relatively better than 3D printing technology. |
3D printers cost less than high-tech multi-axis CNC machines. | The cost of high-tech multi-axis CNC machines is higher than 3D printers. |
Here is an article about the difference between CNC machining and injection molding.
Chapter 2
Types of CNC Machines
CNC machines are primarily categorized into two parts such as:
- 3-Axis CNC Machines, and
- Multi-Axis CNC Machines
These are further categorized into several parts. All these types of CNC Machines are discussed in the section below:
3-Axis CNC Machines
In 3-axis CNC machining, the machine is operated in three-axis (x, y, z). This machining system is easy to operate. It is lower in cost and provides a limited range of movement. The parts need to be re-oriented manually. For this reason, there may be a risk of error and it also increases the cost.
There are two common types of three-axis CNC machining such as CNC Turning and CNC Milling. Both operate in the subtraction process. In both types, a solid block (job/workpiece) is transformed into the desired shape.
CNC Turning
CNC Turning machine is capable of rotating the workpiece during the operation. It is also called a lathe machine and consists of a lathe at the center. It helps to manage and transfer the workpiece programmatically.
In the turning process, the workpiece is held by a chuck and rotated programmatically. The main principle of CNC turning is to operate the cutting tool on the rotating workpiece and create the desired shape. The main parts of a lathe machine are:
- Bed
- Headstock
- Tailstock
- Carriage
- Main spindle
CNC Turing machine or lathe machine is used for straight turning, drilling, taper turning, parting, knurling, thread cutting, etc. of instrument parts. Lathe machines can be used to create a variety of circular, cylindric solids and flat surfaces and to cut screw punches or helixes. The basic process is:
- At first, the G-Code is generated from the designed model. G-Code is a series of code sequence which helps to transform the CAD model into an actual design.
- Then a cylindrical-shaped workpiece is loaded into the CNC machine. The workpiece starts rotating on its own axis. The rotating speed is programmed by the operator.
- The cutting tool starts to trace the rotating workpiece and then subtract material from the solid and bring out the desired shape.
The 3-axis CNC turning machine can make cylindrical parts. Non- cylindrical parts can also be made using a multi-axis lathe machine.
Merits
- Faster than the milling machine.
- The installation process is easier than the milling machine.
- Cheaper than any other CNC machining.
Demerits
- Less versatile than the CNC milling machine.
- Need to reposition parts manually.
- High risk of error.
CNC Milling
CNC milling is the most popular 3-axis CNC machine type. It also uses a rotational cutting tool to remove the material from the workpiece. Metals or metal alloys such as Titanium, Bronze, Steel, Copper, Aluminum, etc., and plastics can be shaped by CNC milling. It is used to make sculptures, car parts, cabinets, rocket components, instruments, etc.
As different materials have different properties, the working capability of the milling machine is dependent on the cutting tool selection, feed rate, RPM, etc. CNC milling machining parts are suitable for use widely across the world. The step-by-step CNC milling process is:
- A 3D model is transformed into a G-Code using fusion360, AutoCAD, or Solidworks. G-Code commands are read by the interpreter of the machine.
- The workpiece is then placed onto a base. Perfect alignment and positioning are very vital to create an accurate shape.
- In a CNC Milling machine, there is a column that holds all the machine components together. The machine interface is situated on the column. It loads, initiates, and executes the G-Code.
- The RAM is located at the top of the milling machine. It is connected with the column. It holds the cutting tool by a spindle. The RAM is also adjustable.
- The rotating speed of the cutting tool is measured by the RPM unit.
- Multiple passes are required to obtain the proper shape. In starting passes, the workpiece is shaped with lower accuracy.
- After several finishing passes, the final product is obtained. This process is repeated to form the desired shape.
- The next stage of milling is to deburring the workpiece. In this process, the defects on the edges are subtracted.
Types of CNC Milling
There are four types of milling such as
- Plain Milling: It is also called slab milling. In this milling, the cutting tool is located parallel to the workpiece. It is used to make a plain surface.
- Face Milling: In this milling process, the cutting tool is located vertically with the workpiece surface. It is used to create various shapes.
- Angular Milling: This milling process is kind of a midpoint between face milling and slab milling. The cutting tool is located angularly with the workpiece surface.
- Form Milling: It is a versatile milling process. In this milling process, different tools can be used according to the shape required.
Merits
- In CNC milling, a large variety of shapes can be obtained.
- It is used to make high-precision metal parts of engineering designs.
Demerits
- Costlier than the CNC turning.
- Need to reposition parts manually.
Check out this article about the top CNC milling aluminum service supplier in China.
Multi-Axis CNC Machines
Multi-axis machines work the same as CNC milling and turning. The main difference is that they come with two additional axes which enhance their capabilities of working and create more creative shapes.
Though multi-axis machining is more effective. The main disadvantage of this machining is the additional cost and hiring an expert operator. Different types of multi-axis CNC machines are:
Mill-Turning
The Mill-turning machine is more advanced than the CNC turning and milling machine. It provides more speed than the CNC turning machine. This machine performs more versatile operations when compared to the CNC milling machine.
Mill-turning machines are capable of making more creative shapes from the workpiece. It provides five-axis milling. Mill turning is suitable for cylindrical workpieces. The working procedure of the mill turning machine is similar to the lathe machine. The main difference is, it works on a five-axis.
The workpiece is held by a spindle which is rotated and fed to the cutting tool. The cutting tool traces the rotating workpiece and removes material from it.
Merits
- The cost of the Mill turning machine is less than the other five-axis CNC machines.
- The production capability of this machine is higher.
- More speedy.
- Varieties in design.
Demerits
- Restrictions in tool access.
- Works well only on cylindrical parts.
Continuous 5-Axis CNC Machining
Continuous 5-Axis CNC machining works just like the indexed 5-axis CNC machine. It is an upgraded version of the indexed CNC machine. At the time of machining, it allows simultaneous 5-axis rotation. It delivers a more complex and precise design than the other 5-axis machines. But the cost of this machine is the highest.
The most complex parts of any manufacturing company are designed by using this machine. Specialist operators are required to operate this machine. It leaves minimal machining marks in the workpiece.
Merits
- The obtained result is of high quality.
- Automatic re-orientation of parts.
Demerits
- Tool access restrictions.
- Very costly.
Indexed 3 + 2 Axis CNC Machining
The working procedure of the indexed 3 + 2 Axis CNC machine is similar to the CNC milling machine. It works on the five-axis. It is faster than the CNC milling machine. This machine is capable of reorienting the solid workpiece.
In this machine, the bed and the tool head are rotatable which performs milling on the solid workpiece from multiple angles. Thus it can build a more complex shape with higher accuracy in less time. It is more costly than the CNC milling machine. It provides automatic repositioning of the workpiece.
The indexed 3 + 2 axis CNC machine is suitable for finer features of the design. But it is not applicable for parts that don’t need more contour control such as housings, jigs, fixtures, etc.
Merits
- Automatic reorientation of parts.
- Obtained results are well featured.
Demerits
- Pricey than the 3-axis CNC machine
- Restrictions in tool access
Chapter 3
Design Guide for CNC Machine
The field of CNC machining has a lot of capabilities. To utilize these capabilities to the fullest, designers must know some manufacturing rules for CNC machining.
There are some CNC machining design restrictions, some general design rules as well as some rules regarding undercuts in case of designing a part for CNC machining. All of these sections are discussed below in this chapter.
Design Restrictions for CNC Machining
Though there are a lot of flexibilities in CNC machining design, there are also a few restrictions. These restrictions are directly connected to the process of cutting, the tool, and the workpiece.
Tool Access
In general, the tool of a CNC machine starts cutting a workpiece from its outer surface. If there is a complex area that requires cutting then it is hard for the tool to access that part. If a location is not accessible at all then that part cannot be machined.
This is why, a designer must design a part by aligning cavities, holes, or vertical walls of the part to one of the main principal directions. If a large depth is required to cut but the part has lower width then the tool access is also an issue here.
In this case, the accuracy will reduce because there will be more vibration on the tool due to using a longer shaft. It is recommended (by CNC experts) to use a tool that is short in length but has a wider diameter.
Tool Geometry
Generally, CNC machining tools have a cylindrical shape with a small cutting length. The cylindrical shape of the cutting tool always causes a curved corner in the workpiece. No matter how small the cutting tool is there will always be a rounded edge on the workpiece which may or may not be visible to the eyes.
Tool and Workpiece Stiffness
Both the cutting tool and the workpiece in CNC machining have a limit of taking load or force. This limit is the stiffness of these components. If this limit is crossed then deformation occurs in those components. So it is very important to supervise the applied load or force on these components while designing the parts for CNC machining.
Work Holding
The designer should keep in mind the fact about the work holding devices that are applicable to hold the workpiece in CNC machining while designing a component. A component should be designed in such a way that it can be fitted in the work holding devices neatly and can withstand the force of the work holding devices.
CNC Machining Design Rules
There are no standards set by the manufacturers for designing a part that can be manufactured by CNC machining. But the most common practices that manufacturers all around the world follow are mentioned here:
Internal Edges
A part can have two types of internal edges such as floor radius and vertical corner radius. The recommended floor radius size is 0.5 to 1 mm and the vertical corner radius is ⅓ times the cavity depth or more.
If a part is machined with end mill tools then there is no need to have any vertical or floor radius clearance. But in the case of ball end tools, the recommended radius is necessary.
The recommended vertical corner radius helps to give better surface finishing on the part. The higher the corner radius the better the surface finishing will be.
Pockets and Cavities
The recommended cavity depth is 4 times the cavity width. A deeper cavity will cause vibration on the tools and will result in poor surface finishing. If a cavity depth is 6 times the tool diameter then it is a deep cavity. In this case, a special tool is necessary for cutting.
Holes
If a part is required to have holes then the hole size should be equal to any standard drill bit size. The minimum recommended hole diameter should be 2.5 mm. But it is feasible to cut a hole that has a diameter of more than 1 mm.
The maximum hole depth should be 4 times the nominal diameter. But it is feasible to have a hole depth of 40 times the nominal diameter. Typical maximum hole depths are usually 10 times the nominal diameter.
End mill tools or drill bits are suitable to cut holes in a part in CNC machining. Holes with tight tolerances are polished with boring and reaming tools.
Minimum Wall Thickness
For metal parts, the minimum recommended wall thickness is 0.8 mm. But the feasible thickness is 0.5 mm. For plastic parts, the minimum recommended wall thickness is 1.5 mm and the feasible size is 1 mm.
Lower wall thickness than the recommended size will cause vibrations and reduce the stiffness of the part. This will not only result in poor surface finishing but also reduce the dimensional accuracy.
Threads
The minimum thread diameter should be M2 or 2 mm and the recommended size is M6. The M2 size can be achieved by using dies and taps. But to achieve the M6 size CNC threading tools should be used.
The minimum thread length should be 1.5 times the thread diameter but the recommended size is 3 times the thread diameter. The first few teeth of a thread usually take most of the load. So, it is unnecessary to use a thread length of more than 3 x diameter.
Tolerances
It is impossible to achieve the exact dimension hence tolerances are appliable to achieve the acceptable dimensions. In CNC machining the standard tolerance for a part is +/- 0.125 mm. But it is feasible for Sunrise Metal to reach the highest precision tolerance of +/-0.0015(JIS B6336) with Makino Brand CNC machines.
Letterings and Texts
The recommended font size for text or lettering in CNC machining is 20 or higher. The thickness of the cut or rise of the text should be 5 mm. It is recommended to use standard fonts such as Verdana or Arial.
Maximum Part Size
For CNC milling the typical dimension of a part should be 400 x 250 x 150 mm. For CNC turning it should be 500 mm (radius) x 1000 mm. Large CNC machines are capable of producing parts with up to 2000 x 800 x 1000 mm dimensions.
Tall Features
A part should not be extremely tall for CNC machining because it will lead to vibrations. The recommended maximum height to width ratio is 4.
Tips for designing CNC undercuts
If the part is complex then there are some areas that the tools of a CNC machine cannot access. Such areas or corners are known as undercuts. Different types of cutting tools such as lollipop-shaped, V-shaped, or T-shaped tools are suitable in cases of undercuts.
Undercut Clearance
If the undercut is on the internal part then there should be enough clearance between two walls so that the tool can have access. The recommended undercut clearance is 4 times the depth.
Undercut dimensions
It is recommended to give a width of 3 mm to 40 mm for undercuts and the maximum depth should be 2 times the width.
Check out this article to learn more about CNC machining design.
Chapter 4
CNC Machining Material
Not all materials are suitable for CNC machining. For this reason, it is very important to select the right material according to the application of the part. The properties of materials indicate their applicability for CNC machining.
Properties of Materials
The below section shows different materials which are suitable for CNC machining according to different properties.
Hardness
If the required hardness is less than 90 HRB then stainless steel or alloy steel is recommended. It is better to use tool steel if the part needs to have a hardness of more than 50 R C.
Tensile Strength
PEEK, Nylon, and PC are good materials for parts that require low tensile strength (less than 100 MPa). If a part requires medium tensile strength (less than 500 MPa) then Aluminum is a good option. For high tensile strength parts (more than 500 MPa) the best materials are tool steel, stainless steel, and alloy steel.
Chemical Resistance
If a part requires good chemical resistivity then it is better to use PEEK, Teflon, or stainless steel as the raw material in CNC machining.
Temperature Resistance
PEEK, Brass, and Teflon are good materials for parts that require low-temperature resistance (less than 250oC). If a part requires medium temperature resistance (less than 400oC) then Aluminum is a good option. For high-temperature resistive parts (more than 500oC) alloy steel, stainless steel, and tool steel are the best materials.
Machinability
Brass, Aluminum, and POM are easily machinable materials and are good for high-volume productions.
Types of material for CNC machining
The main raw materials for CNC machining should be metals and plastics. But not all metals and plastics are CNC machinable. The metals and plastics which are applicable for CNC machining are mentioned and discussed in this section:
Metals
There are various metals and metal alloys that are suitable for CNC machining. However, they have different characteristics and have a different scope of applications. We have briefly discussed some of the commonly used metal alloys below:
- Aluminum: Al6061 is used in many industries to create electronic and aircraft components. It is favored by manufacturers for its workability, strength, ease of joining, and corrosion resistance properties.On the other hand, Al7075 is used in aerospace industries because of its high strength-to-weight ratio. Though it is not as weldable or corrosion resistive as Al6061 its strength to weight ratio makes it useful for aerospace and many other industries. It is the most commonly used material for CNC Machining. It has excellent machinability and a strength-to-weight ratio. Aluminum parts are naturally corrosion resistive. It has excellent electrical and thermal conductivity. Al6061 and Al7075 are some common aluminum alloys used in CNC machining.
- Brass: It is an alloy of copper and zinc. Brass has excellent machinability and gives a golden appearance that is aesthetically pleasing. It has a good friction coefficient which makes it more stable.
- Tool Steel: It is resistant to abrasion, stiffness, and high temperature. Tool steel has excellent hardness. For this reason, it is suitable for different industrial tooling.
- Stainless Steel: Stainless steel has excellent ductility, strength, corrosion resistivity, and wear resistivity. It is machinable, weldable, and polishable.
- Mild Steel: It is the cheapest of all the metals. Its mechanical properties are excellent as well as its weldability and machinability.
- Alloy Steel: Its toughness, hardness, wear resistance, and fatigue resistance are better than mild steel. But its chemical resistance is not as good as mild steel.
Plastics
As plastics are resistant to chemical reactions and do not possess any electrical conductivity so, these are suitable for various applications. In CNC machining, manufacturers mainly use plastics to make prototypes of a part. The most common plastics used in CNC machining are:
- PEEK: It is an engineering thermoplastic of high performance. It’s suitable for most demanding applications.
- ABS: Among all the plastics it is the most common thermoplastic material which is lightweight and has excellent mechanical properties and impact strength.
- POM (Delrin): This one is the most easily machinable plastic. It has good frictional characteristics as well as high stiffness and excellent thermal stability.
- Nylon: Nylon is a general-purpose thermoplastic with excellent mechanical properties. Its chemical resistivity is also amazing.
- Polycarbonate (PC): Polycarbonate is a strong, thermal resistive, and tough plastic. Its best feature is that it can be transparent and applicable for various outdoor applications.
Visit here to learn about CNC machining for prototyping.
Types of Surface Finishes for CNC Machining Materials
The materials mentioned above require different types of surface finishing in order to achieve better hardness, chemical resistivity, good appearance, and many other improved properties. The below section shows different types of surface finishes done on a CNC machined part:
Silk Screening
This is a cheap way to add logos or text on a CNC machined part. It is available in many colors. It is only applicable to the external surface of a part.
Powder Coating
Powder coating is a process of adding a thin layer of polymer paint that is corrosion and wear-resistant, strong, and protective. It is better than anodizing and compatible with various metals. It’s not suitable for internal surfaces and small components.
Anodizing
This type of surface finishing is mostly for aluminum and titanium parts. It adds a non-conductive, hard, and thin ceramic layer to the surface. It increases the wear and corrosion resistance of a part.
Hardcoat Anodizing
This is similar to anodizing but the layer is thicker in this case. Both anodizing and hardcoat anodizing are suitable for applying on the internal surfaces of a part.
Bead Blasting
Manufacturers use this type of surface finishing to remove tool marks from the surface of a part. They mostly do this to make the part look aesthetic.
Chapter 5
Design Tips for Cost Reduction
The cost of parts production using CNC machining depends on a few things such as:
- Start-Up: The start-up cost mainly depends on the CAD model of the part. This cost is constant for both high volume and low volume production.
- Model Complexity: The more complex the model the costlier it will be to manufacture that part.
- Machining Time: Complex parts will lead to more machining time which will eventually reduce the rate of production. A lower production rate means higher costs.
- Material Cost: Raw material cost eventually adds to the overall cost of manufacturing parts with CNC machining.
It is better to keep the design simple and stick to the standard features so that the overall cost is not too high. Here are a few tips to reduce the overall cost of CNC machining:
Considering Material Cost
When choosing a material for CNC machining the first thing to focus on is the application of the part. Sometimes two or more materials can exhibit the same properties and hence can be used for the same application.
In this case, it is obvious to choose the cheaper one in order to reduce the overall cost. But the quality should never be compromised. Below some metals and plastics are chronologically ordered according to their cost from highest to lowest.
Metals
- Stainless Steel 304
- Brass C360
- Aluminum 7075
- Alloy Steel 4140
- Aluminum 6061
Plastics
- PEEK
- Polycarbonate (PC)
- Nylon (PA 6)
- ABS
- POM (Delrin)
Minimizing Orientations
If a part requires multiple orientations then it will increase the cost of production. Because in this case, manual labor is necessary to manually rotate the part which will increase the labor cost for 3-axis CNC machining.
For multi-axis CNC machining labor costs elimination is possible but the machine itself costs a lot more (about 60% to 100%) than 3-axis CNC machines. So, in order to minimize cost:
- It is better to design parts with the least possible orientation. The best option is to have no orientation at all.
- If multiple orientations are a must then it is better to split the part into different smaller parts and then assemble the parts after manufacturing.
Increasing the Fillet Size
When the fillet size is larger, it is possible to use a larger tool to cut internal edges. In this case, the user can cut more surface area at once which reduces the cutting time. Lower cutting time leads to a higher production rate which means a lower cost of production.
Here are a few tips to follow to increase the fillet size:
- Using the Same Radius: If all the edges have the same radius then there will be no need for tool change. It will save a lot of time.
- Fillets on External Edges: If possible, it is better to keep a small fillet on the external or outer edges of a part.
- 90o Internal Corners: In the case of such corners, it is better to use undercuts according to the instructions given in chapter 2.
- Radius Size: it should be a little higher than ⅓ times the cavity depth.
Limiting Thread Length
Avoiding unnecessarily long threads is a good way to reduce the cost of CNC machining. The thread length can be 3 times the thread diameter which is more than enough. Because longer threads do not improve the connection strength.
Increasing Wall Thickness
If weight is not an issue for a part then it is better to have thicker walls for the part. The thicker the wall the less deformation there will be. It will also be easier to machine without fracturing the part. Moreover, a thicker wall means less waste of material which is good for cost reduction.
Using Standard Holes
Drill bits have some standard sizes which are easily available all around the world. A hole that is not similar to the standard size of a drill bit will be difficult to cut as a special type of tool will be needed to create that hole. The special tool will cost more than regular drill bits which will eventually add to the overall cost.
Avoiding Lettering and Texts
It is better to avoid letterings and texts using CNC machining as it requires complex machine orientations and movements. Costlier CNC machines are necessary to achieve complex movements. To reduce cost, in this case, silk screening (see chapter 3 for more details about silk screening) is a good alternative option.
Chapter 6
How to Start CNC Machining
So far we have talked about how to design parts for CNC machining, which material to choose, and how to reduce the cost of CNC machining. In this section, we will talk about starting manufacturing with CNC machining.
There are a few simple steps that you can follow to start manufacturing parts with CNC machining.
Step 1: Exporting Compatible CAD File to the CNC Machine
There are different types of CAD file formats for CNC machining such as IGES, STEP, SLDPRT, etc. Among these, the most common formats used are the IGES and the STEP formats. The main reason these are applicable is because they are
- Standardized
- Open-Source, and
- Usable across different platforms.
To get the most accurate dimensions in a part, the best option is to directly import the STEP CAD file format from the design software.
Step 2: Preparing Technical Drawing
A technical drawing is a drawing of a part that has a 2D top view, front view, and a side view and all the views have dimensions mentioned in the drawing. The technical drawing helps to clearly understand the part. It also makes it easier to set the raw material in the CNC machine for machining.
A technical drawing provides information that you cannot find in a STEP file. A user will need the technical drawing when:
- One or more surfaces require different types of finishing.
- Any kind of tolerances is mentioned in the design.
- The part contains threads in the design.
Step 3: Starting to Manufacture and Post-Processing
After completing the first two steps all you have to do is start the CNC machine. The machine will automatically start creating or manufacturing the required part.
After finishing the part manufacturing process, you have to do some post-processing works such as surface finishing which is mentioned above for CNC machining.
Chapter 7
Applications of CNC Machining
CNC machining is widely applicable in various manufacturing industries because of its versatility. This process is very cost-effective. Moreover, it is suitable for a large range of materials. So the demand for CNC machining in modern technology is high. It is suitable both for prototyping and in the development stage of any product.
Industries Which Use CNC Machining
The section below shows all the industries where CNC machining is suitable to produce various components.
Space Industry
Creating parts for space application is very complex and costly. CNC machining technology is suitable for making these parts. This machining technology is perfect for creating space equipment because it provides top-notch material properties and precision.
CNC machining also offers a large variety of surface treatments to the space parts. For example, CNC machining was used by KEPLER for creating equipment for the satellite.
Automotive Industry
The automotive industry uses CNC machining mostly to make high-tech vehicles. This technology ensures the high performance of the designed parts. For example, CNC machining was used by a renowned Dutch company named PAL-V to make personal land and air vehicles.
These are the world’s famous flying vehicles. They choose CNC machining because it is good for prototyping. And the resultant output of CNC machining is quite promising as this technology can use varieties of materials.
Aerospace Industry
CNC machining is very suitable for making lightweight parts. So, this industry widely uses this technology]. CNC machining creates aircraft products that come with great physical properties and tight tolerance. This machining technology is also applicable in the developments stage of aircraft products.
A renowned Ph.D. researcher team of the Delft University of Technology had used CNC machining technology to make their modeled aircraft engine. Their main purpose was to develop the efficiency of the propeller engine. And they were successful.
Motorsports and Sports Industry
Motorsports and sports industries use CNC machining to create necessary equipment for their vehicles. Sports cars or bikes should be lightweight and durable. CNC machining helps to achieve these features.
For example, the Swedish company named Cake used CNC machining to build their high-performance electric motorbike. They customized each of the parts of that bike using CNC and so the products were up to the mark. The company was able to achieve its desired quality using CNC machining.
Industrial Manufacturing and Tooling
A wide range of materials is suitable for CNC machining. Plastic materials are also applicable as the workpiece in CNC machining. Various plastic manufacturing industries use this technology to create various designs of plastic items and tools. Manufacturers customize the CNC machine molds and use them to create these items.
For instance, the renowned manufacturing company Precious Plastic have used CNC machining to transform waste plastic materials into iPhone phone case. Manufacturers also use CNC machining for the fabrication of various tools.
Electrical and Electronics Industry
Electronics components manufacturers use CNC machining to create a prototype and also manufacture electronics gadgets. Electronic equipment requires some compulsory features such as electrical insulation, heat dissipation, etc. CNC machining provides all those features.
The TPAC company used CNC machining technology to manufacture their specialized electronic sensing system. They use anodized aluminum to build up their custom model.
Hardware Industry
Manufacturers in this industry can design and developed custom metal products using CNC machining. The designed product comes with higher dimensional accuracy. CNC machining also plays an important role in the functional prototyping of the design.
For example, the DAQRI design team prototyped their AR (Augmented Reality) hardware equipment by using CNC machining and customized all the parts of that hardware. They used CNC machining because it reduces the manufacturing costing and the resultant output was quite impressive.
Musical Instruments Industry
CNC-produced equipment has a great precision capability. Musical instruments are quite complex and need more accuracy. For this reason, musical instruments industries use CNC machining technology. Musical instruments manufacturers can make the instruments from any material. So CNC machining is a great option.
Defense and Healthcare Industry
Military industries frequently use CNC machining for prototyping and building the necessary parts of their weapons. Manufacturers in the medical industry create various medical materials such as surgical instruments, implants, orthotics, etc. using CNC machining.
CNC machining can produce tight tolerance items which are affordable and give high performance.
Check out more about CNC machining for medical devices at this link.
Chapter 8
CNC Machining Manufacturers
Revolution came in the manufacturing industries all around the world with the introduction of CNC machining. Nowadays most of the top manufacturing companies use CNC machines to manufacture various parts for different industries and sectors.
However, there are many manufacturers who manufacture CNC machines and supply them globally. The below list shows a few top global CNC machine manufacturers:
- Datron AG (Germany)
- Okuma (Japan)
- Mazak (Japan)
- BCAM CNC (China)
- Blue Elephant (China)
- Vmade CNC (China)
- Powermatic (USA)
- Bolton Tools (USA)
Tips to Find the Right CNC Machine Manufacturer/Supplier
Different CNC machine suppliers have different capabilities or qualities. They may or may not match your concern. However, there are some things that you must keep in mind in order to find the right supplier/manufacturer.
- If you are willing to purchase a machine from a global supplier then you must choose a supplier who holds a good supply chain management system globally. Because most suppliers usually focus on their own country even though they supply globally.
- Manufacturers’ experience is a very important part. An experienced manufacturer/supplier will always provide good quality products and their customer service will also be excellent.
- This is an era of technology. So, it’s very important that the manufacturer or supplier you choose has the ability to produce goods with advanced technologies rather than using old ones.
- There are different types of CNC machines. Some suppliers focus on a single type rather than manufacturing all the types. They do this in order to make sure their product gets the best quality. If you are willing to purchase a single type of CNC machine then these are the kinds of suppliers you should choose.
- Sometimes you may have to get different types of CNC machines and also save the purchase cost. In this case, the best option is to choose a supplier who manufactures different types of CNC machines and supplies them.
Chapter 9
CNC Machining Services
Though CNC machining is a standalone manufacturing process manufacturers often combine it with other manufacturing processes to make the product quality better. Companies that provide CNC machining services may also provide many other manufacturing services.
Some companies, such as Sunrise Metal, provide CNC machining services along with Die Casting, Rapid Prototyping, etc. A CNC machining service providing company should have the following capabilities:
- They must have the ability to give cost-saving suggestions and also technical proposals regarding parts manufacturing.
- The facilities should have modern advanced multi Axis CNC machines with high precision.
- They must have high-quality inspection instruments such as spectrometers, X-Ray detectors, advanced measuring machines, etc.
- CNC machined parts require various surface finishings. So a CNC machining service providing company should provide different types of surface finishing services as well.
- Timeliness is a very important cost-relating factor. A company should always be able to provide on-time delivery whether it’s low volume or high volume production.
Top Global CNC Machining Service Providing Companies
Different companies have different capabilities when it comes to CNC machining. Some companies only provide the CNC machining service but some companies provide CNC machining along with other manufacturing services.
However, the below list shows the top CNC machining service providing companies globally:
- PRECISE Tool & Mfg. Inc. (USA)
- PROTOLABS Manufacturing (USA)
- Sunrise Metal (China)
- FIRSTPART (China)
- 3ERP (China)
- STAR RAPID (China)
- Xometry (Germany)
These are some of the few top global CNC machining services providing companies. But there are many more companies around the world. However, these companies are the best because all of them hold the above-given capabilities.
For example, Sunrise Metal works with a wide range of materials for CNC machining such as stainless steel, aluminum, copper, different types of plastics, etc. Sunrise metal also provides different types of surface finishing services for CNC machined parts such as wet painting, anodizing, e-coating silk printing, powder coating, etc.
Moreover, Sunrise Metal contains advanced CNC machines such as the Mazak 7 Axis Milling & Turning Machine, CNC Lathes, Sodick Wire Cutting Machine, Surface Grinder, EDM Machine, etc. in different facilities.
Chapter 10
Conclusion
CNC machining is an excellent manufacturing process for low volume, medium volume, and high volume production as well as for one-time production. It’s the best manufacturing process for creating prototypes of parts and also testing various properties and performances of those parts/prototypes.
This process provides the tightest tolerances. So, if the parts require such tolerances CNC machining is the best option. Here are a few final tips for designing parts for CNC machining:
- Try to keep the fillets as large as possible for internal corners.
- Try to align the main design features along the principal axis.
- Make the design of the parts in such a way that standard tools are usable.
- Cavity depth shouldn’t be larger than 4 times the cavity width.
- A part containing both threads and tolerances should have a technical drawing for the operator.
Hopefully, these tips and all the information above will help to understand CNC machining and also ease up the designing process of the parts for CNC machining.